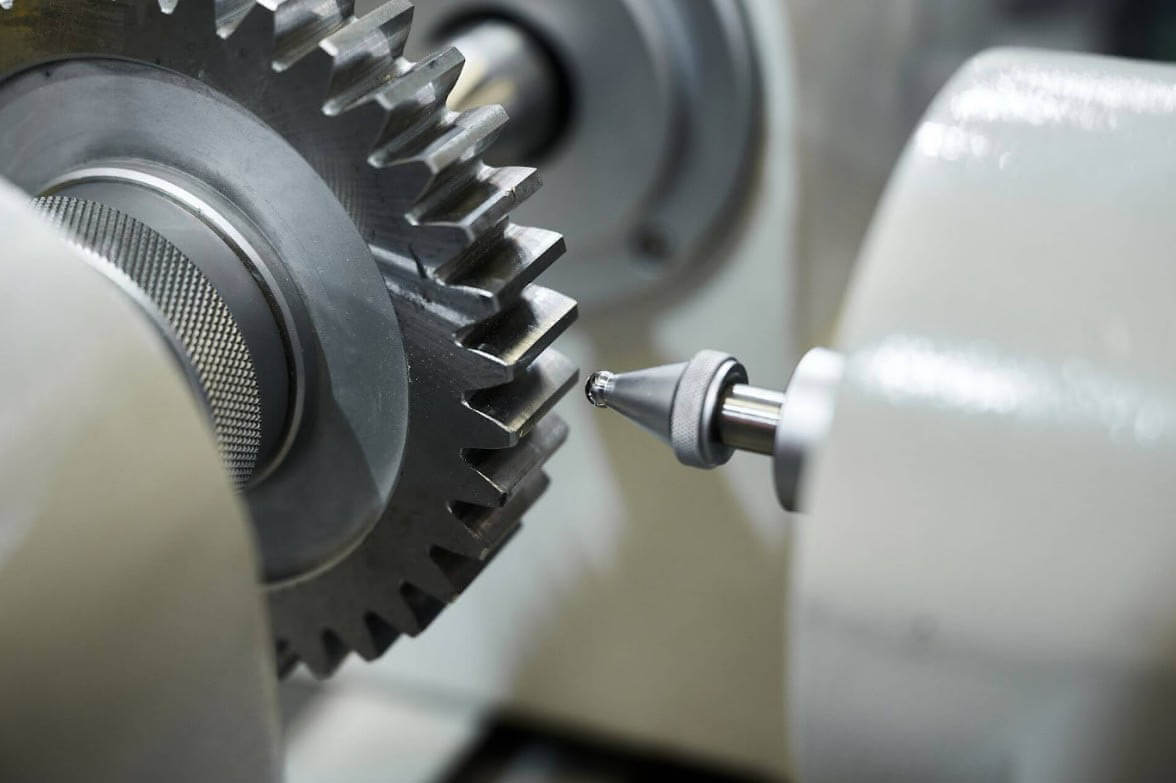
For any machine system with moving parts, proper lubrication is a must, as the repeated wear and tear caused by friction can eventually damage the fragile components of the machinery. Depending on the type of machinery, users will sometimes apply lubricants such as oil or grease manually, which can be a time-consuming process and may be impractical for more large-scale projects. For this reason, they may also choose to outfit their equipment with an automatic lubrication system, which can make the manufacturing process faster and more efficient, though, it is not without its drawbacks.
In the following blog post, we’ll discuss the pros and cons of automated lubrication as part of machinery maintenance. We’ll outline the benefits that these components may provide for end users, as well as any downsides that may be present. Finally, we’ll help you to weigh these considerations for the needs of your particular machinery, helping you to make an informed decision about whether or not they are right for your application.
Automated Lubrication: How It Works
The regular, continuous motion of machinery parts creates friction, which generates heat and causes wear and tear to the components of the equipment. Over time, this mechanical stress becomes cumulative and will eventually weaken the elements of the machinery that are subjected to it. The use of chemical lubricants, which usually consist of natural or synthetic oil or grease, helps to reduce friction by creating a thin barrier between two machinery parts. This reduces the amount of heat generated and protects the machinery, extending its lifespan.
In an automatic lubrication system, a pump is used to deliver a predetermined amount of lubricant material to the machinery parts. This can be done through a manually entered command or, more commonly, using a timer. While there are many different versions of the delivery systems for an automatic lubrication system, the key consideration is that the correct amount of lubrication is applied to all of the necessary elements of the machinery.
Pro: Automatic Lubrication Improves Efficiency
For most industries, efficiency is absolutely crucial to remaining competitive and maintaining continuing success; this means achieving maximum results based on the energy input that’s given. According to the Society of Tribologists and Lubrication Engineers (STLE), friction and the wear and tear caused by friction are responsible for the loss of up to one-third of the energy produced by machinery.
Automatic lubrication is one of the most effective ways business owners can address this issue, as it improves the efficiency of their technology. Reducing friction is the key. However, if the lubrication is applied manually, the machinery must be shut down and operations halted for as long as it takes for it to be applied. Continuously stopping and restarting the equipment is a major cause of lost time in many industries.
Con: Increased Up-Front Costs
An automated lubrication system should be considered an investment, one that has a significant up-front cost that will pay off over time. When choosing whether or not to undertake this investment, business owners should consider all the potential expenses that come with installing this feature in their machinery.
The cost of the parts themselves is only one element. There is also installation and labor, the added maintenance costs of the new system, and the expense of any customization that may be required for specific machinery. It’s recommended users weigh these expenses against the projected long-term savings that will result from installing an automatic lubrication system in machinery.
Pro: Reduced Wear on Machinery Means Lower Maintenance Costs
The cost of maintaining machinery is always a major consideration for any industry, and one of the key benefits of automatic lubrication systems is their impact on this bottom line. As mentioned above, the wear and tear that occurs as a result of friction is cumulative and will eventually lead to more serious damage. Of course, as part of the regular maintenance process, this damage is typically repaired as it occurs. However, a machine that is more effectively lubricated will incur less damage and therefore require fewer repairs. The machine will also be less likely to break down unexpectedly, which further contributes to the lower maintenance costs that come with an automatic lubrication system.
Con: Automatic Lubrication May Increase the Complexity of the System
Depending on which type of system is used, automated lubrication can increase the complexity of a machine significantly. It can add multiple new moving parts and require regular refills for the lubricant reservoir. This added complexity may not be ideal for users who wish to keep things simple. However, it’s worth noting that not all automatic lubrication systems are necessarily complex ones. A single-point lubrication system, for instance, requires only a few added parts while still providing benefits for many different types of machines.
Pro: Improved Labor Savings
For many businesses, an automatic lubrication system can directly translate to reduced labor costs, largely because the system handles a job that would otherwise have to be performed by a human worker. Without automatic lubrication, the work of applying oil to the moving parts of the machinery would be completed by a paid laborer. Bypassing this allows human resources to be redirected to areas where they are more useful and, thus, saves on labor costs.
Con: Automatic Lubrication Is Not Compatible with All Systems
Each type of machinery has its own needs, and not every automatic lubrication system is compatible with every type of machine. The requirements of different technologies may vary based on both the lubricants used and the availability of space and power for an automated system. It’s possible the machinery needed for certain industries will not lend itself to the installation of these types of lubrication systems.
It’s worth noting, however, that this issue can often be mitigated through the use of specialized, custom equipment, which our engineers specialize in at Aberdeen Dynamics. If you have a specific need for your business, we will walk you through your options so that you can maximize the efficiency and cost savings of your equipment.