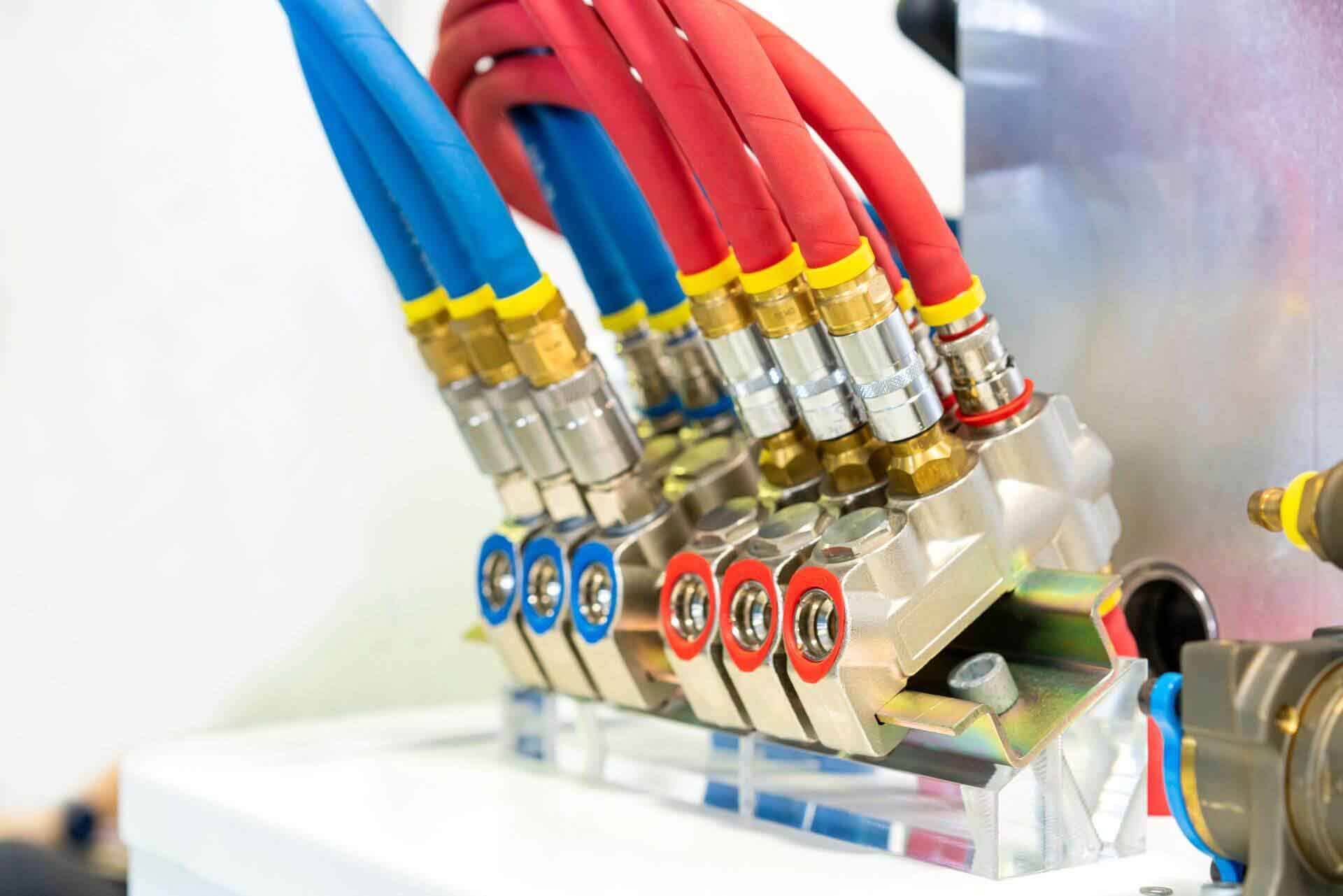
Pneumatic technology is the backbone of many industries, with its ability to generate power at high speeds being critical for everything from manufacturing to agriculture. By utilizing pressurized air to create movement in mechanical systems, pneumatic devices provide a cost-effective method for performing the precise, repetitive tasks that thousands of modern businesses rely on.
These systems, however, only remain reliable as long as they can transfer air throughout their component parts without losing pressure due to leakage. For this reason, pneumatic hose fittings have become the unsung hero of modern industries: It’s these fittings that ensure secure and efficient airflow throughout the machinery they are a part of.
In the following article, we’ll offer a guide to the most common types of pneumatic hose fittings, including their applications, benefits, and compatibility with different hoses and equipment.
Pneumatic Systems: The Basics
As mentioned above, air transfer is the key principle behind the operation of a successful pneumatic system. In a pneumatic device, a pump draws air into a reservoir and pressurizes it. When the operator activates the device, a valve opens to allow this compressed air to enter the pneumatic cylinder through a system of reinforced hoses. As the air attempts to expand back to atmospheric equilibrium, it places force on the pneumatic actuator, causing it to move with a high degree of speed and power.
Since pneumatic systems depend so heavily on maintaining a certain level of air pressure, a weak point in any of the elements can compromise them and cause them to lose much of their efficiency. Often, these weak points occur at connection points, such as where the hoses connect to the actuators. For this reason, manufacturers have poured a great deal of research and development into improving the reliability of the fittings between the hoses and other components.
Hose Fittings: What You Need to Know
Well-constructed pneumatic hose fittings must meet several specifications. First, and most importantly, they must prevent any air leaks, as these can hamper the effectiveness of the system. They must also be able to withstand the conditions the machinery will be subjected to, often including heat, moisture, or the presence of potentially corrosive substances. Proper fittings will allow operators to perform the tasks required of them quickly to maintain effective and efficient operation.
When choosing a hose fitting for a specific application, operators must also consider the availability of space, the speed at which they may need to switch the hoses, and the specific application the fitting will be used for. Different conditions will impact the functionality of different fitting options.
Quick-Connect Fittings
Quick-connect fittings are excellent for meeting the above criteria because they utilize spring-loaded connections to create instant seals when they are attached or removed. This allows the fitting to be snapped on and off quickly without any pressure loss that could cause the pneumatic actuation to operate less effectively.
In many fast-paced working environments, pneumatic hoses must frequently be attached, removed, and switched around, making quick-connect fittings the ideal option for them. Because they do not make use of any clamps or other intrusive parts, quick-connect fittings are excellent for rubber hoses and other flexible materials. Applications that make the best use of quick-connect fittings include assembly-line conveyor belts and automotive paint applicators.
While they are ideal for many applications, however, users should also consider that there are certain situations where quick-connect fittings are not the optimal choice. For example, if the system will be subjected to stresses from vibrations or other movements, then it is possible for these hose fittings to break free or for the small rubber and metal elements on the interior to easily wear out and become damaged.
Push-to-Connect Fittings
For operators whose hose fittings must be suited to low- or medium-pressure situations, push-to-connect fittings may be the ideal choice. These fittings are extremely easy to install, as they can be pushed directly onto hoses without the need for any glue, screws, or clamps. Instead, these fittings contain a grab ring on the inside that secures them to the outside of the hose. As they are more compact than quick-connect fittings, push-to-connect fittings are better suited for areas with less space.
The most common applications for push-to-connect fittings are in transportation, where they are used for inflating tires and related tasks, and in smaller-scale construction tasks, such as in pneumatic drills and nail guns. These fittings are best suited for thinner materials such as plastic, as they put less strain on the hoses than more heavy-duty materials.
Barbed Fittings
Equally useful for a wide number of applications, barbed hose fittings have the benefit of being inexpensive and easy to manufacture. Constructed from stainless steel or brass, barbed fittings have ridges (or “barbs”) that are inserted into the pneumatic tubing. The barbs grip the interior of the hose, creating a seal that prevents leaks from occurring. While these hose fittings cannot be switched as easily as quick-connect fittings, they do not contain any component parts that can wear out, rendering them more inexpensive and potentially longer-lasting than the fittings listed above.
Barbed fittings are commonly used for applications that may be subjected to stressors that could damage push-to-connect or quick-connect fittings, including marine systems, plumbing, and other areas that could expose the fittings to corrosive chemicals. At Aberdeen Dynamics, we design pneumatic systems for a variety of applications, and we have experience with every type of pneumatic hose fitting and material. If you have questions about the best fit for your specific needs or you wish to inquire about a custom project, contact us today. Our expert team of engineers and technicians will help guide you to the best pneumatic setup so your operation works more efficiently and effectively.