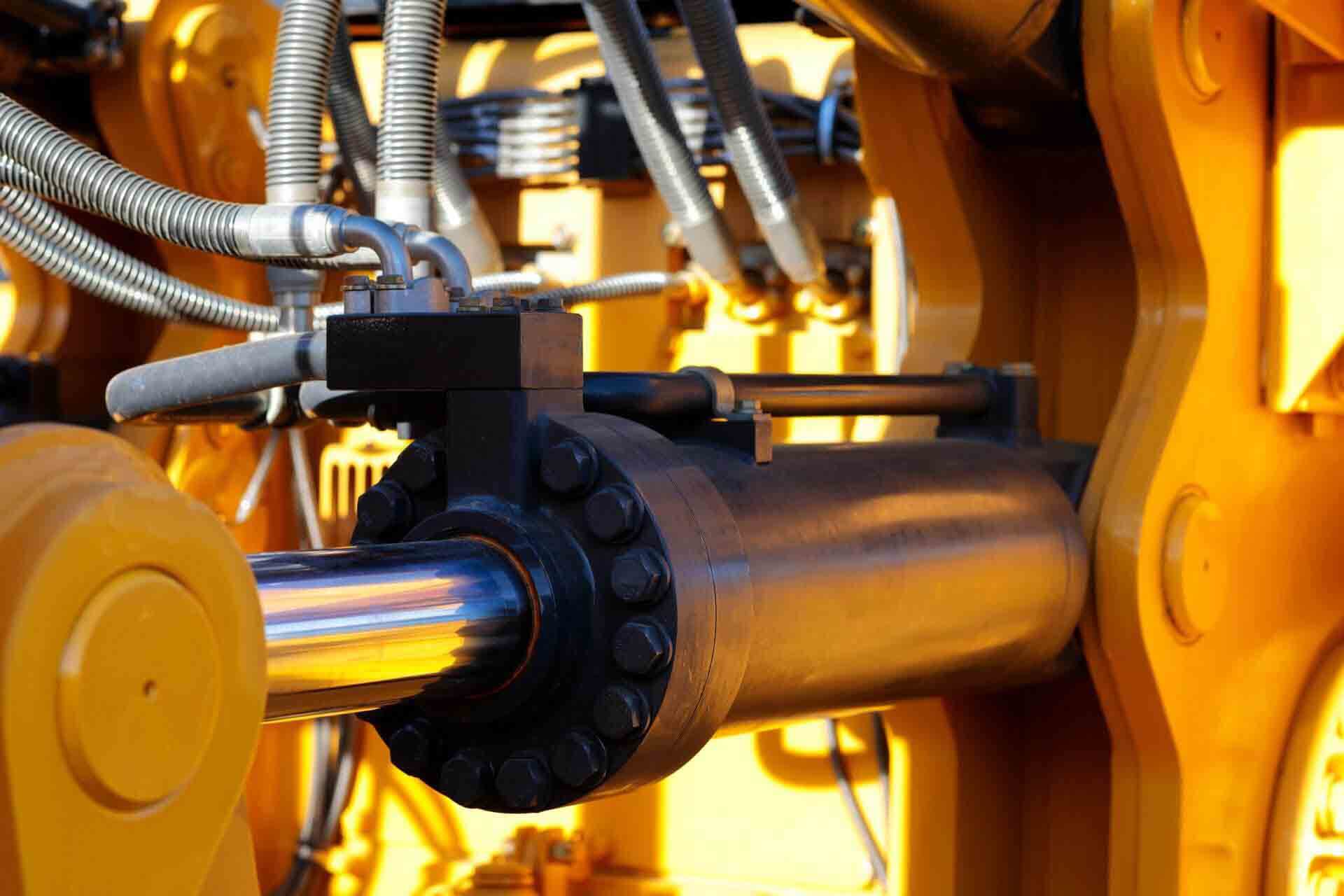
Actuators require mechanical force to operate, and there are several methods of generating that force. The most common and reliable ones are pneumatic and hydraulic systems. While the basic concept behind both is the same—each one utilizes a pressurized medium in order to create motion and generate power—they also differ in key ways, and each provides different advantages for different applications.
In the following article, we’ll compare and contrast pneumatic vs. hydraulic systems, helping you to determine which is best suited to the specific requirements of your application.
Pneumatic vs. Hydraulic: What’s the Difference?
While the mechanism by which they operate differs, the fundamental physical principle underlying both pneumatic and hydraulic actuators is exactly the same. Pascal’s Principle states that pressure applied to a single point in a contained fluid is transferred throughout the entire container. This means that if a pressurized liquid or gas enters the system, the pressure will build up and ultimately create the required movement in the actuator. Pascal’s Principle allows mechanical actuators to generate an incredible amount of force, provided the mechanical parts are well-constructed and up to the task.
The primary difference between pneumatic and hydraulic systems is the type of fluid medium used to generate the motion. In a pneumatic actuator, a pressurized gas (such as compressed air) is used. In a hydraulic actuator, the medium is a liquid. Any incompressible liquid can do the job, but in modern applications, it’s usually oil.
The first thing you may note when comparing the two is the fact that hydraulic systems specifically depend on the liquid medium being incompressible. For pneumatic systems, the opposite is true (consider that they utilize compressed air). This means that they operate somewhat differently. Hydraulic fluid transmits pressure without really affecting the liquid itself, while pneumatic gas seeks to expand back to its original pressure after being compressed, essentially acting as a powerful spring. Which of these two features is preferable depends a great deal on the user’s specific needs.
Which Is More Powerful?
If your application requires a very high level of force, then hydraulic actuators are the way to go. That’s because the incompressibility of the hydraulic liquid means that a vastly greater force output can be achieved than is possible for pneumatic technology. Common pneumatic actuators rarely utilize more than 150 psi or so, while hydraulic technologies can utilize pressure levels in the thousands or even tens of thousands of pounds per square inch.
This means that hydraulic systems are much better suited to heavy lifting applications, including in the construction, automotive, and aviation industries. This is true for other sectors as well. If you require an actuator to move a great amount of weight, a hydraulic system is almost certainly the best option.
What About Speed?
For some tasks, speed is the goal, rather than raw power. If that’s the case, pneumatic actuators are the clear winner, as the compressibility of the gas medium used means that the mechanical energy can be generated, and the system can return to equilibrium, much more quickly. Oil, the primary fluid used in hydraulic systems, tends to flow very slowly, while air will move quickly to fill a space where it’s introduced. Gasses simply move faster than liquids, a fact that pneumatic systems take advantage of. Compressed air moves through valves and piping with minimal lag time, allowing pneumatic systems to respond very quickly to commands.
The speed of pneumatic systems makes them excellent for automated manufacturing and production. Materials in factories are often both constructed and packaged using pneumatic technology. High-speed pneumatic systems also have applications in the food and beverage industry, the shipping industry, and many others that require high-speed and relatively low-weight loads.
Which Is More Energy Efficient?
When it comes to energy efficiency, there are many factors in play that will affect which type of actuator is the best to use. All other things being equal, hydraulic systems tend to be more energy efficient, once again due to the incompressibility of the liquid medium. Because air and other gasses can be forced into much smaller containers, a pump system must work that much harder to bring them to a pressurized state. This means that these pumps will tend to utilize a great deal of energy, unlike liquids, which can transmit more force with a comparatively lower input.
Of course, other factors will also impact the efficiency of your system. For example, the overall complexity of the technology can greatly affect its energy usage. If precision is important in a more complicated piece of equipment, hydraulic systems may be the best due to the added control they offer. However, depending on the nature of the job, pneumatic systems may be able to achieve more work in less time because of their superior speed, saving on energy costs in this way.
Cost and Other Factors
If cost is a major consideration for your application, then it’s worth noting that pneumatic systems don’t require purchasing a specialized medium to operate. Many simply use air, which can be freely acquired from the surrounding atmosphere. On the other hand, if your application makes use of hydraulic technology, you will periodically need to purchase and replenish the hydraulic oil or other medium. The relative complexity of hydraulic actuators also tends to make them cost more than their pneumatic counterparts.
Environmental factors are also worth considering when considering pneumatic vs. hydraulic actuators. If compressed air leaks from a pneumatic system, it will dissipate harmlessly in the atmosphere. If oil leaks from a hydraulic system, however, it must be cleaned up in order to reduce the risk of environmental damage. Last, but certainly not least, in our list of considerations is the build quality of the equipment itself. The benefits of both hydraulic and pneumatic systems cannot be fully achieved with inferior materials or design, which is why we recommend the high-performing, top-quality motion control systems designed and manufactured at Aberdeen Dynamics. Whatever your application is, we can help you to design and implement the perfect system for the job.