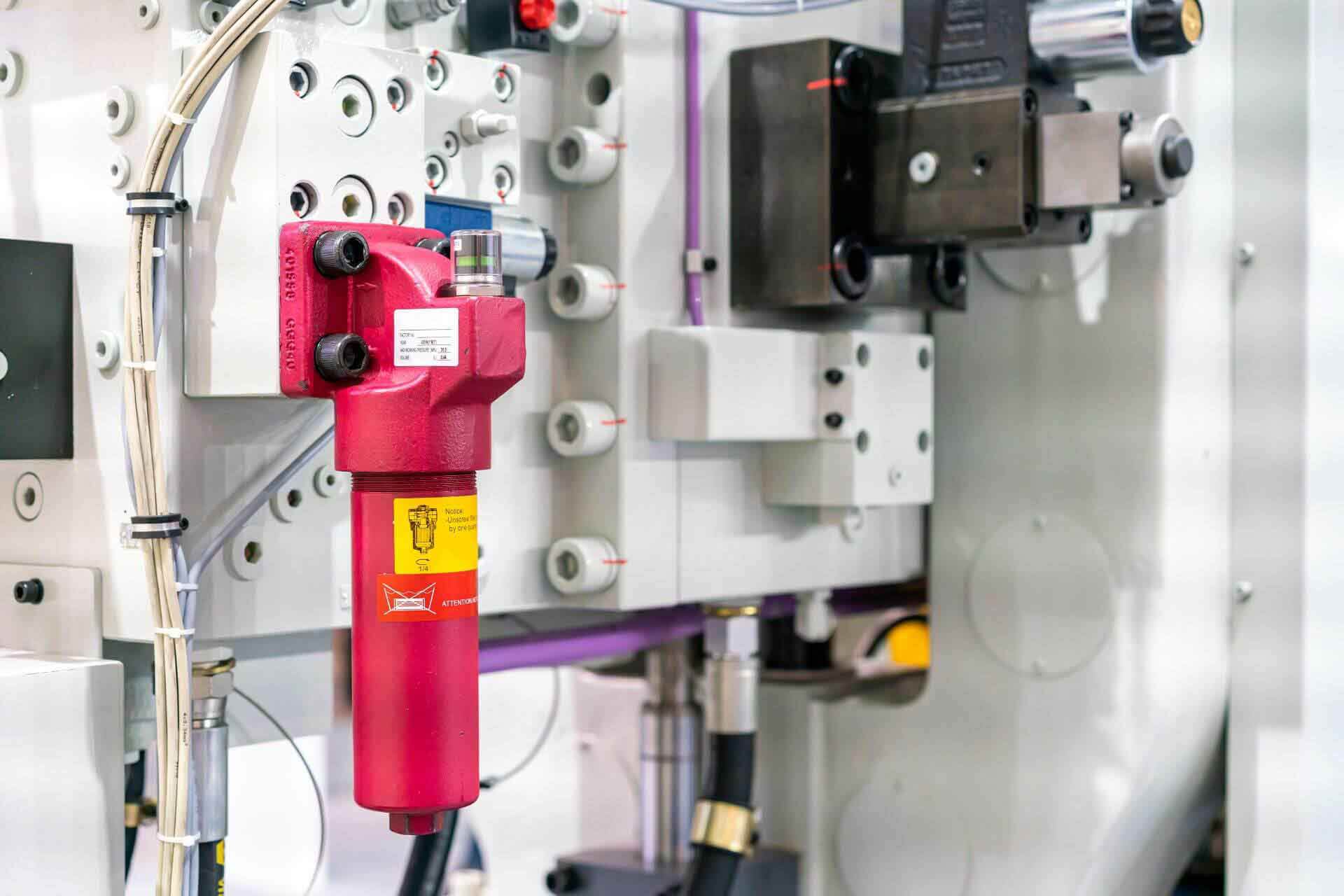
Hydraulic systems are among the most powerful machines in humanity’s arsenal, being utilized for such grand-scale projects as the construction of skyscrapers and the exploration of space. They are used to move loads weighing hundreds of tons and to provide resistance against some of the most intense forces on the planet. As mighty as they are, however, hydraulic systems are still vulnerable to contamination from the smallest sources: Even a fleck of rust or a drop of water can begin to compromise the effectiveness of the technology.
For that reason, anyone who works in an industry that depends on this type of machinery understands the importance of a well-constructed, reliable hydraulic filter. The following discussion of basic practices for filter maintenance in hydraulic systems will help you improve the efficiency and extend the lifespan of the machinery you rely on.
The Importance of Fluid Management
Hydraulic systems use internal fluids—usually oil—to generate the power they need to perform their essential tasks. Properly maintained, they are extremely effective. However, over time, particulates can gradually build up in hydraulic fluids, generating friction and heat and causing wear and tear on the interior of the system. Chemical contaminants and moisture can also hamper the efficiency of a hydraulic system. Regardless of the source of the contamination, it can eventually diminish the performance of the machinery and ultimately cause a costly breakdown in the system.
A good filtration system is a key element of hydraulic fluid management, which keeps the oil clean and free of moisture or chemicals that could affect its ability to generate motion in the system. There are multiple filtration methods for hydraulic systems, which are selected based on the application and pressure levels.
Hydraulic Filters: How They Work
Different filtration methods are used depending on the pressure levels in the hydraulic system. For example, low-pressure systems can make excellent use of return-line filters or suction filters, while commonly named pressure filters can be used for more heavy-duty systems. Kidney loop filters combine both pressure filters and return line filters to split the workload and clean hydraulic fluids more economically.
To prevent contaminants from being introduced into the hydraulic components of a machine, a layer of porous material can be used to capture them as the fluid makes its return journey to the reservoir in which it is stored. The material used as the porous layer varies based on the type of hydraulic fluid used and the application of the machinery.
Whether it’s composed of steel mesh, fiberglass, cellulose paper, or another porous material, this layer forms the basis for the hydraulic filtration system, which can utilize either suction or the natural flow of the liquids through the system to eliminate the presence of foreign substances in the hydraulic fluid. A metal support structure helps to maintain the shape of the filter as it is subjected to the high pressures present in a hydraulic system. Rubber gaskets are also present to prevent leaks.
Many filtration systems also feature a bypass valve in case the filter becomes clogged. This prevents potential blockages that can damage the system. However, it also allows unfiltered fluid to circulate within the hydraulic mechanism.
Filters Should Be Replaced Regularly
Small particles and other contaminants are introduced every time your hydraulic machinery is used. This is simply a result of the day-to-day operation of the equipment. The materials used to make hydraulic filters are highly efficient at catching these foreign substances, but over time, they build up within the filter. Gradually, the filter becomes dirty and less efficient, leading to a greater degree of wear and tear on the machinery and its internal components. Ultimately, it may become blocked entirely, necessitating the use of the bypass valve.
To ensure the ongoing reliability and longevity of your hydraulic system, it’s essential to replace the filters regularly. To ensure this is done in a timely manner, keep an eye on the pressure in your system. If the pressure starts to drop, this could be an indication that your filter is starting to fail and in need of replacement.
You will want to ensure you change the filter long before the bypass valve activates (or if you do not have a bypass valve, the filter simply fails entirely). By replacing filters at regular, timely intervals, you can prevent any system efficiency loss due to an oversaturated filtration system.
Regular Inspections Are a Must
Of course, the filters themselves are not the only elements in a hydraulic system that are susceptible to eventual failure. Many other elements, including the rubber gaskets and the seals that prevent leakage, will inevitably begin to degrade over time. You can largely prevent the damage to your machinery that will result from this by investing in regular, proactive inspections of the equipment, either performed by your employees or by an outside technician who specializes in your type of machinery.
In most cases, an inspection will include replacing the filters before they become too saturated with contaminants. It will also include a check of the rubber gaskets and other elements that prevent leakage. The pump that circulates the fluid through the filter is also checked, ensuring that it is operating in peak condition. If necessary, repairs can be made to keep the hydraulic system working reliably and mitigate any damage that has occurred.
Ensure Your Hydraulic Filter Is Suited for Its Task
Ensuring your hydraulic filter operates effectively is a matter of regular maintenance and care, with a particular emphasis on keeping the filters clear of a harmful buildup of particulate matter. However, another key factor in improving the performance and extending the lifespan of your hydraulic system is ensuring that you have the correct filtration system for the task that is being performed.
As mentioned above, the appropriate filtration system will depend on the amount of pressure the system utilizes, as well as other factors, including the potential presence of abrasive chemicals that may corrode the rubber gaskets and other elements of the machinery. The best method for ensuring you have the correct hydraulic filter for your application is to invest in a custom system that is tailor-made for your operation’s specific needs.At Aberdeen Dynamics, we specialize in creating these custom parts, as well as any replacement fixtures that may be needed to maintain the ongoing and effective operation of your hydraulic systems. Contact us for more information and to discuss your options.