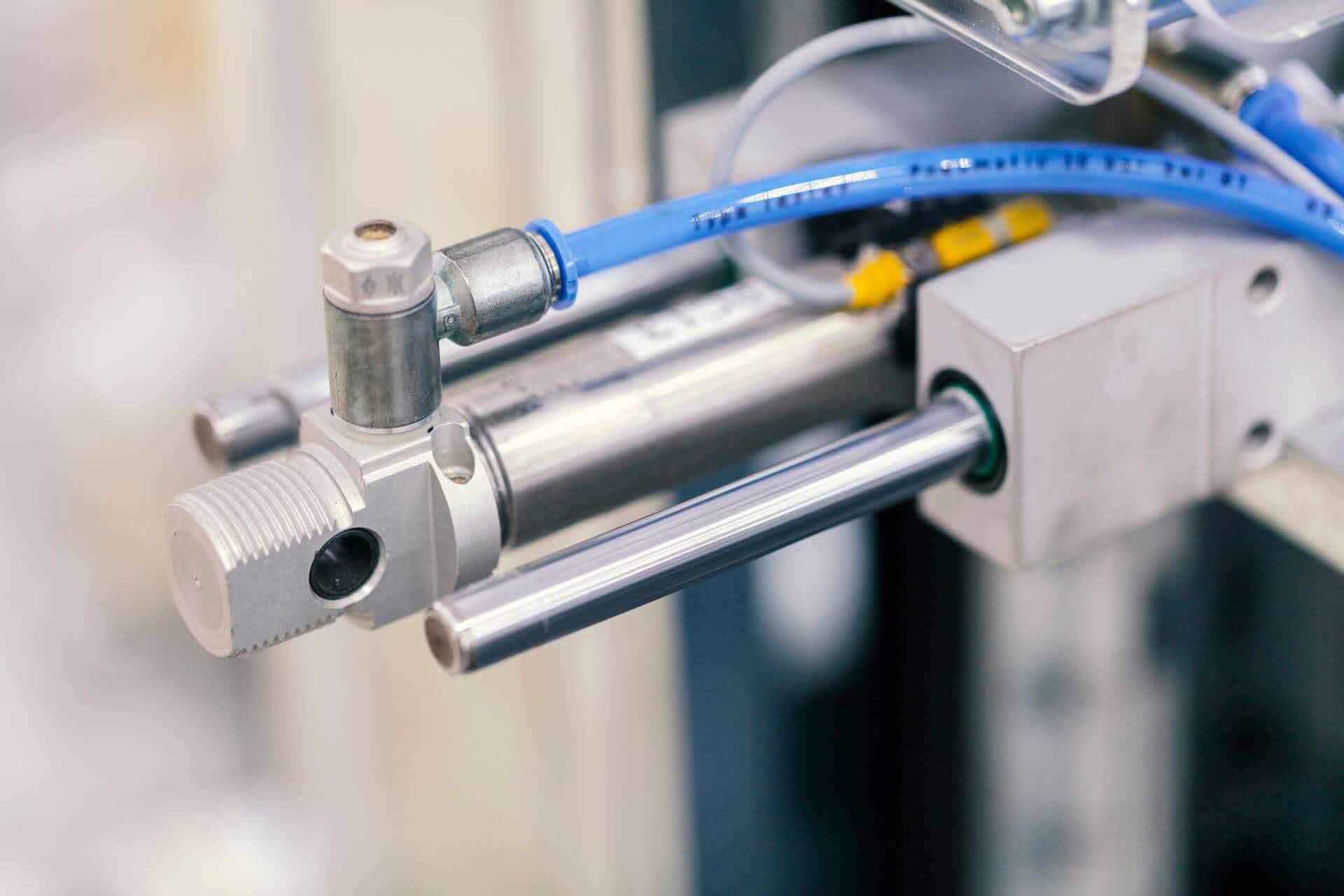
Pneumatic actuators are a crucial component of many different types of industrial equipment, providing a powerful, efficient, and low-cost method of generating movement. Designed to use compressed air to create motion, a well-crafted and properly installed actuator is often the linchpin of the operation that depends on it. However, as with any mechanical device, a pneumatic actuator must be properly maintained to achieve optimal performance.
In the following post, we’ll offer a few of our best tips for troubleshooting and maintaining your pneumatic actuator in order to improve its efficiency, improve its output, and extend its life span.
Pneumatic Actuators: An Overview
The term actuator refers to a device that is designed to generate motion. This can be circular, as in a rotary actuator, or straight, as in a linear one. Actuators can be used for any component of a machine that requires moving parts. They are commonly found in heavy construction equipment, as well as in automobile engines, manufacturing machinery, robotic assembly lines, and countless other commonly used technologies.
A pneumatic actuator, specifically, is one that utilizes compressed air as the source of its mechanical energy. Pressurized air contains a great deal of potential energy, which, when strategically released through a controlled valve, can be transferred into pistons, cylinders, and other actuator components to achieve motion.
Actuator Maintenance: The Basics
The actuators in a technological system work extremely hard, generating torque or thrust for hours on end as they perform their function. While they are both durable and reliable, they are subject to the same sort of wear and tear as other mechanical systems. Keeping them in peak condition is a matter of attention to detail. Periodically shut your machinery off to check its component parts for the following issues:
1. Check for Signs of Corrosion or Damage
The repetitive use that pneumatic actuators are subjected to may eventually cause the component parts to wear out or crack. Commonly, this may occur in the piston rods or cylinder barrels, although other elements are also vulnerable. Corrosion is another common issue. Metal components may develop rust, especially since compressed air may encourage water vapor to accumulate in certain areas. Rust can weaken the system and ultimately cause it to fail, so check that there are no corroded parts in your actuator and repair or replace them if there are.
2. Replace Worn or Damaged Seals
Since pneumatic actuators depend on pressurized air to perform their work, it’s crucial that strong seals exist between hoses, valves, pistons, and other parts. If these seals begin to become worn, air leaks can develop, which in turn can cause the device to fail to achieve the necessary pressure. As a result, your actuator will not be able to generate the necessary force and will no longer operate as efficiently, if at all. Regularly inspect all seals on your pneumatic actuators to ensure they remain in excellent shape.
3. Ensure Proper Lubrication
When it comes to machinery with moving parts, friction is the enemy, causing parts to wear out prematurely and reducing the overall longevity of the device. Proper lubrication, ideally with machine-grade mineral oil, will go a long way toward reducing repair costs and extending the overall lifespan of your machinery. Effective lubrication of actuator parts will also reduce the corrosion mentioned above, further improving the efficiency and longevity of the device.
4. Remove Contaminant Buildup
Over time, a buildup of contaminants can also hamper the effectiveness of your pneumatic actuator. The most common sources of contamination are dirt and grime, excess oil, and even pieces of rust from corroded parts. These contaminated parts can do a great deal of damage, eventually causing pistons, rods, and other elements to break down entirely. Periodically cleaning the machinery and wiping away any buildup of contaminants is an easy but critical way to ensure your actuator operates as effectively as possible.
Troubleshooting a Pneumatic Actuator
Even if they are properly maintained, pneumatic actuators are occasionally subject to problems. A few of the most common ones are listed below, as well as what you can do to fix them.
The Problem: Air Pressure Dropping
If your actuator is failing to generate the force necessary to perform its job optimally, it may be due to a reduction in the air pressure. Most pneumatic devices have gauges to inform you if the pressure has dropped to suboptimal levels. There are several reasons why this may occur. It may be due to a worn seal, as mentioned above, or it may be due to a leak in a hose. It’s also possible the valve is stuck in the open position, possibly due to a buildup of debris. Patching any leaks and clearing any buildup may resolve issues with air pressure.
The Problem: Actuator Is Not Receiving Power
Even an immaculately maintained actuator will not perform its work effectively if it doesn’t receive a proper supply of power from its energy source. If your machinery entirely refuses to switch on, it may be due to the fact that the power supply is, for one reason or another, not reaching the device. Power down the machine and then check wiring connections and replace any faulty wiring so that the actuator can receive the power it requires to operate.
The Problem: The Actuator Is Overheating
Another common problem with actuators is overheating, which you can usually detect by a burning smell or by unusual noises coming from the machinery. Often, overheating is caused by improper lubrication, which leads to excess friction. Properly oiling the components of the actuator can eliminate this problem. If not, the issue may also be caused by clogged filters or other buildup. Ensure that there are no contaminants hampering the movement of air in the actuator.
Get the Best Equipment You Can
Ensuring your machinery always operates at optimal levels is also a matter of having access to high-quality, well-crafted parts. By investing in the best technology in the business, available from Aberdeen Dynamics, you’ll be able to take advantage of efficient, long-lasting, and effective pneumatic actuators.