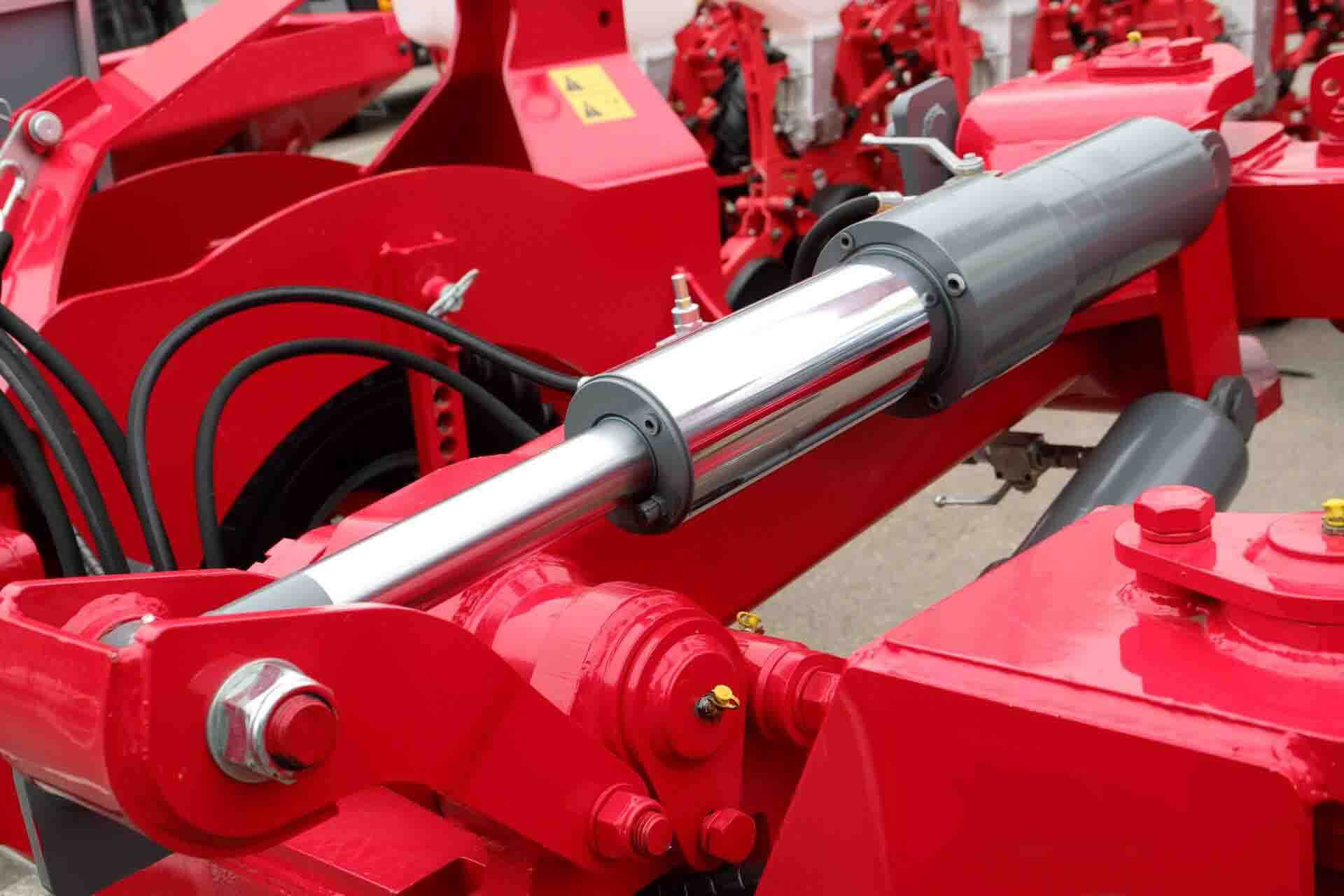
Hydraulic actuators are a vital component of dozens of different types of machinery, found in everything from airplanes to heavy construction equipment to common household technologies such as swimming pool pumps. A well-constructed and maintained actuator is a powerful and reliable workhorse, continuously providing motion control and lending mechanical advantage to the equipment it is installed within. As with any machinery component, however, actuators occasionally face operational problems that hamper their ability to perform their required functions effectively.
In the following blog post from the experts at Aberdeen Dynamics, an Oklahoma-based company dedicated to the design and production of high-quality, specialized machinery parts, we’ll discuss some of the most common hydraulic actuator problems and what you can do to address them. We’ll also help you to determine when the issue is serious enough to necessitate contacting the professionals.
The Problem: Low Hydraulic Pressure
Hydraulic actuators operate by way of pressurized fluid, which allows them to multiply force to bring a great deal of power to bear for their required tasks. If, for any reason, your hydraulic system is not able to build or maintain the necessary pressure, you may find its output is greatly reduced. This issue can usually be diagnosed by using handheld pressure gauges, which can help you to read if the fluid pressure is lower than it should be for optimal operation.
The Solution: You May Have a Faulty Compensator
One of the most common reasons for low pressure in a hydraulic system is a faulty compensator. The job of this element of the system is to keep the pressure at a constant level, compensating for changes in the flow from the pump. In many cases, the compensator becomes stuck in an open position, causing the pressure to dip below the necessary levels. Ensuring your compensator spool is operating effectively may help to restore full pressure to your system.
The Problem: Leaking Oil or Other Fluids
Another common cause of low hydraulic pressure in your actuator is a fluid leak—most modern actuators use oil as their medium. However, occasionally, other fluids may also be used. This is often one of the easier problems to diagnose because a fluid leak is generally visibly apparent. The machinery may feel slick to the touch with oil, or you may notice dripping coming from the device. Occasionally, the signs of a leak are also more subtle. If you suspect one but cannot detect it on your own, a professional may be able to introduce a UV dye to your hydraulic actuator, which will allow them to detect even small and less obvious leaks.
The Solution: Replace Damaged Gaskets
There are several components that work together to contain the fluid inside the hydraulic actuators in your machinery. Most actuators utilize gaskets or O-rings to create seals. These may become worn out and lead to leaks developing in the machinery. Replacing these parts may solve the problem, provided you ensure that a tight seal is created when you install the new ones.
Note that other, more serious issues may also lead to a leaking actuator. For example, damage to the valve itself can have a similar outcome but will likely require the assistance of a professional to repair it.
The Problem: Contaminated Hydraulic Fluid
Another common—and serious—problem that is often faced by hydraulic actuators is the presence of air or foreign material in the hydraulic fluid. This can cause multiple deleterious effects, including damaging the interior of the machinery and necessitating costly repairs. Air in the machinery can also cause major problems, as it can limit its ability to create the necessary compression.
You can often detect this issue if you notice a burning smell coming from your equipment. This could be the result of chemical reactions due to foreign materials in your fluid. If the hydraulic fluid begins foaming, this may also indicate the presence of air in your actuator.
The Solution: Contact a Professional to Flush the System
A contaminated hydraulic actuator is a problem that is likely to require professional attention, as they may need to utilize specialized equipment to clear out the foreign material. The first step is to remove the contaminated fluid; the system will likely need to be drained entirely. The next step is to remove any accumulated contaminants. This can be done by flushing the system with a cleaning fluid, although your maintenance professional may also need to remove larger buildup by hand.
The Problem: Power Source Failure
Problems with your hydraulic actuator may lie in other elements of the system. Some actuators are powered by an electrical motor, and a short circuit or other electrical problem can cause them to fail to operate. Poor connections in the solenoid circuitry may cause the actuator to fail to communicate properly with the rest of the machine. This can also lead to issues with operation.
The Solution: Clean Corroded Connections and Replace Faulty Wiring
The electrical issues that arise with actuators are addressed in much the same way as similar problems that plague other machinery parts. Over time, wiring connections can become corroded, preventing a steady flow of electricity through the system. Wiring can also become loose or damaged. This will need to be repaired before the system can once again be functional.
Remember that working with electrical connections can be hazardous. The machinery should be fully powered off before you attempt to clean any elements. If you, or a member of your team, are not trained to perform electrical work, then contact a professional to perform this task.
If You Just Can’t Fix the Problem
It’s possible, of course, that you’ll discover your hydraulic actuator problem is not so easy to address, or it may recur despite your best efforts. When this happens, it’s time to call in assistance with the repairs.
It also may not be that you have failed to troubleshoot effectively; it might simply be the result of utilizing low-quality equipment. If you discover that you can no longer rely on your actuator technology, you should consider replacing it with something that is crafted to a higher standard. For professional repairs or to discuss investing in top-quality equipment that will stand up to the hard work you are demanding, contact Aberdeen Dynamics.