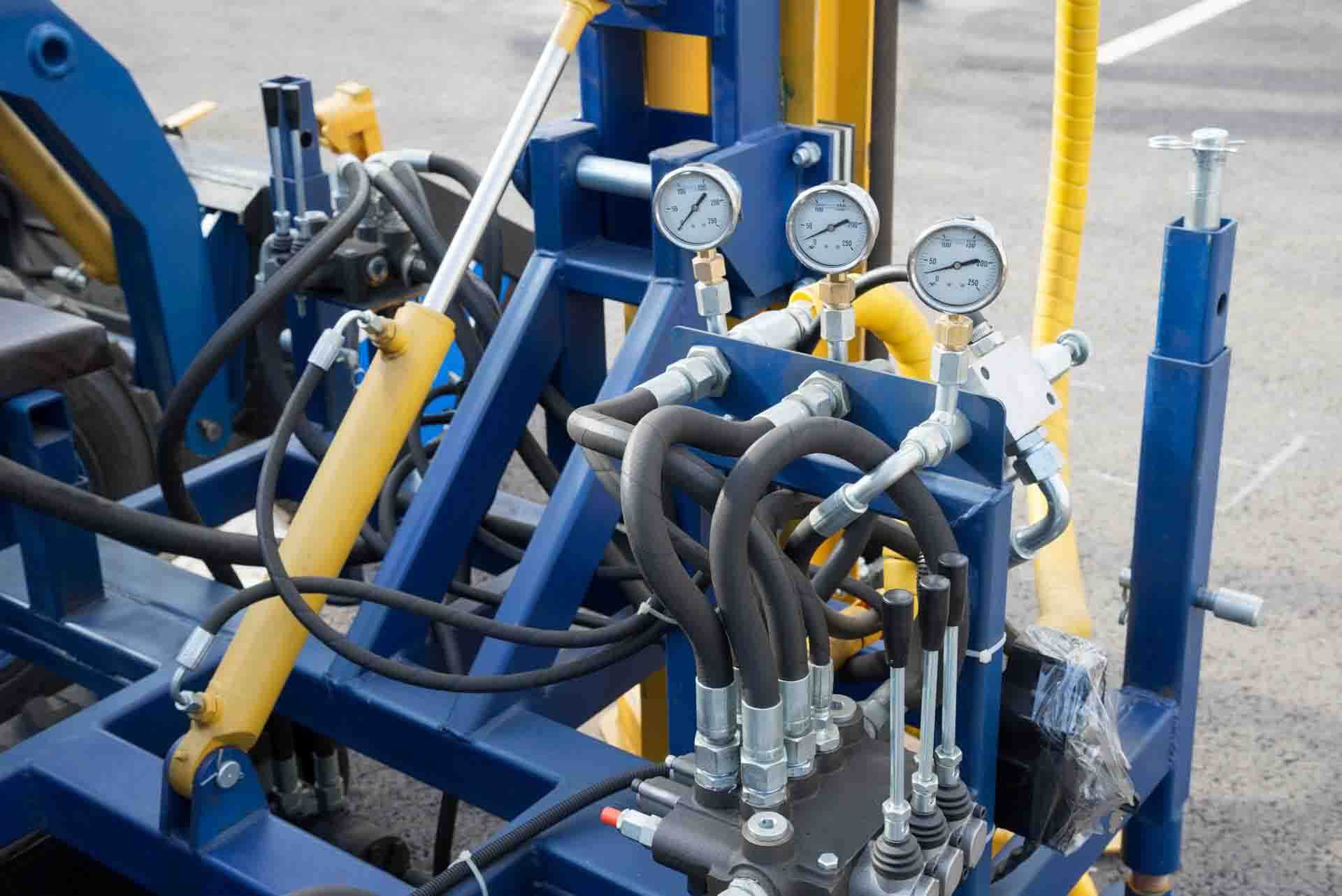
Precise and reliable fluid conveyance is a required feature of many types of industrial machinery, particularly those that utilize hydraulic technology. Ensuring the safe, efficient, and effective operation of hydraulic equipment is a matter of installing the correct hose assemblies. Failure to do so can do more than just hamper the ability of the machinery to perform its job correctly. It can also lead to damage and eventual deterioration of the component parts. This can ultimately result in increased maintenance costs and may necessitate costly replacements.
Specifying hose assemblies, however, is often easier said than done. There are multiple elements to doing so successfully, which can be broken down using the mnemonic acronym STAMPED. In the following blog post, we’ll explain what the STAMPED acronym means and why each aspect is critical for specifying hose assemblies.
S for Size
The first element to consider is the sizing of the hose itself, which has a major impact on the flow of the fluid medium being used. A hose with a diameter that is too large will fail to produce adequate pressure, leading to sluggish operation. Conversely, a hose with a diameter that is too narrow will likely become too pressurized, which may lead to equipment damage. The length of the hose also matters, as a hose that is too short or too long may not fit on the machine at all.
To size a hose properly, several pieces of information are needed: the inner diameter, the outer diameter, and the length. This information is usually available when purchasing a segment of hose, but it can also be measured using a caliper specifically designed for the task.
T for Temperature
Different types of hydraulic systems operate at different temperatures, and the required hose assemblies must be adapted to match. Hoses are not interchangeable in this regard since they are constructed from various materials, such as rubber, metal, or plastic, that have different tolerances for withstanding temperature extremes. The operating temperature of the machinery itself must be considered, as well as the ambient temperature in the surrounding environment.
Note that the hose assembly refers not just to the hose itself but to the fittings and other connecting parts as well. Users should check the manufacturer’s ratings for all the component parts to ensure that the entire system operates effectively.
A for Application
Another one of the most important considerations for specifying hose assemblies is their application: that is, what exactly the assembly will be used for. This is critical because this aspect affects the hose’s environment, the various stresses it will be subjected to, and its accessibility for maintenance.
To offer an example of what we mean, consider that hydraulic systems are frequently installed in machinery for the oil and gas industry. This means they will continuously be subjected to high temperatures and other stressors. A hose assembly used in these industries, and related ones, will need to be constructed from materials that are resistant to high temperatures in order to prevent damage. If not, maintenance for these assemblies will be more frequent and more costly.
M for Media
The medium being transported through the hose is another critical factor when specifying hose assemblies because, once again, not all hoses are equal in this regard. Hoses used for water must be rated differently than those used for oil or other fluid conveyance. Some hoses are required to convey dangerous or corrosive chemicals, and they must be able to do so safely without placing the equipment at risk. Remember also that this applies to both the hose itself and all fittings and couplings connected to it.
To ensure a hose assembly can handle the medium being conveyed, users should familiarize themselves with the manufacturer’s chemical compatibility chart, which is often available on their website.
P for Pressure
Users must also familiarize themselves with the pressure ratings of the hose assemblies they utilize in their machinery. They must be kept well within safe operating parameters in order to minimize the risk of damage to the equipment. The concern is not just that the pressure may go too high—known as burst pressure—but that it could go too low as well, causing the hose to be crushed by the pressure differential in the atmosphere. This is known as collapse pressure, and users must be aware of it when specifying hose fittings.
As you might expect, pressure is affected by the other elements of the STAMPED acronym. For example, a different ambient environmental temperature will greatly affect the pressure in the system. This must be taken into consideration when installing hose elements.
E for Ends
As we’ve previously mentioned, it’s not just the hose itself that must be taken into consideration when specifying hose fittings. Every part it is connected to—referred to in the acronym as the Ends—must be equal to the task to which the system is subjected. Hose fittings and couplings must also fit perfectly in the overall setup. Those that are too large or too small for the element they are connected to will not operate as effectively.
Ideally, all the parts that make up the assembly will be specifically designed to match up with one another. If they do not, users will need to carefully research each part so that they can ensure all the ends work together smoothly.
D for Delivery
Finally, delivery is the aspect of STAMPED that ties everything else together, as it refers to the actual physical delivery of the parts, including their creation and installation. This is the element we specialize in at Aberdeen Dynamics, as our responsibility is to create customized fluid conveyance systems for our clients. We consider each element of the STAMPED acronym to create hose assemblies that function effectively for every possible fluid conveyance system and then deliver them to our clients as a complete package.